Manufacturers Put Measures In Place To Stop The Spread Of Covid-19
MaryBeth Matzek | Insight PublicationsInsight Publications | Safe quarters
Talk about foresight. In January, just as the world was learning more about COVID-19 and what was happening in China, Waupaca Foundry created a cross-functional team to plan steps the company would take if the virus arrived in any of the states where it operates.
The COVID-19 action teams created a step-by-step approach along with an implementation plan to keep Waupaca Foundry running, says Jon Loken, the company’s director of safety and health. That planning has paid off.
“We developed a sequence of what we would do at different points (as state rules changed) and have followed that,” he says. “As we have gone on, we have felt prepared.”
Waupaca Foundry is just one of the hundreds of manufacturers in the New North trying to balance keeping their operations running while maintaining the safety of their employees. Most manufacturers have been deemed essential businesses, so they remain open through Wisconsin’s Safer at Home order.
The Occupational Safety and Health Administration, together with the Centers for Disease Control and Prevention, spells out the steps employers must take to protect their workers against COVID-19. In addition to encouraging social distancing, frequently disinfecting personal and common workspaces is essential to stopping the virus. If it can be shown an employee contracted COVID-19 at work, it is counted as a reportable OSHA incident.
Federal rules also require employers to encourage workers to stay home if they are not feeling well and prohibit penalizing them for doing so. To stop the disease spread, an addition to the Family and Medical Leave Act provides extra protection to workers who need to take time off if they are sick or must care for a sick relative or for a child due to school or day care closure.
To keep its employees safe, Waupaca Foundry implemented several changes in early March as more Americans were diagnosed with COVID-19, including implementing social distancing, changing the rules on respirator use, disinfecting workstations and installing hands-free door openers. It also began staggering work shifts to reduce congestion in the cafeteria, locker rooms and other areas. In addition, it installed Plexiglass dividers where workers couldn’t be 6 feet apart.
With plants in Waupaca and Marinette and in Michigan, Illinois, Indiana, Kentucky and Pennsylvania, Loken says it was vital to put the new safety standards in place company-wide.
“Communication with our workers has been important. We started back in early February about what was happening, and as changes have gone into place, we’ve explained them,” he says. “We want to help them understand these changes are all about preventing the spread of the virus.”
Loken says the last step of Waupaca Foundry’s safety plan — daily temperature checks and requiring all employees to wear masks — will kick in if an employee tests positive for COVID-19. “We hope that it’s something we can prevent,” he says.
WHEN WORKERS GET SICK
While some manufacturers use automation and robotics, which can help keep workers spread out, others don’t have that luxury. At meatpacking plants, for example, employees work in close quarters. Three meatpacking plants in Brown County — American Foods Group, JBS USA Holdings Inc. and Salm Partners — have reported COVID-19 outbreaks.
JBS Packerland temporarily closed its Green Bay plant in late April after nearly 300 workers — about a quarter of its employees — became sick with the coronavirus. After President Trump ordered meatpacking plants to stay open in the first week of May, JBS Packerland reopened and said all employees will be tested for the virus before they can begin working again
American Foods Group, also in Green Bay, had more than 175 employees test positive for the virus as of the end of April. The company has not spoken publicly about steps it’s taken to stop COVID-19 from spreading in its plants.
When an employee tested positive for COVID-19 at Salm Partners in Denmark, company leaders quickly added more safety measures to keep other employees safe.
“Our primary goal is to protect our partners, community and customers,” says Keith Lindsey, president and CEO of Salm Partners. “Food production has been identified as an essential industry in our country, and we need a healthy workforce to continue producing products to feed the nation. We are enacting all measures at our disposal to ensure the safety of our people and the food supply of our nation.”
Salm Partners has added several health protections to keep its workforce of about 500 safe, including using a single entrance for all employees and visitors so temperatures can be checked, increasing the number of buses that bring employees to Salm to ensure social distancing and requiring all employees to wear face masks while in the plant. Lindsey says the plant’s common areas, such as the lunchroom, are being cleaned more frequently and the chairs and tables are spread farther apart to maintain social distancing.
Salm Partners also took the step of offering free, voluntary COVID-19 testing, in coordination with the Brown County Health Department, to all of its employees to not only create peace of mind for workers but also to help halt spread of the virus.
“We felt that testing would help identify people who carry the virus but show no symptoms and help our partners feel safe that the majority of people they’re working with have tested negative for the virus,” Lindsey says.
About 35 workers tested positive. They were sent home with pay to self-quarantine for 14 days.
Brown County Executive Troy Streckenbach credits Salm Partners for testing its employees — a step few others have taken.
“This is an extraordinary step and I want to thank them for prioritizing the testing, as it has allowed them to recognize people carrying the virus without symptoms, which helps protect the health of their people, their families and the Brown County community,” he said in a statement.
TRAINING TIME
While postsecondary schools were closed for in-person classes, Northeast Wisconsin Technical College kept its North Coast Marine Manufacturing Training Center in Marinette open. The training provided for employees and contractors needed to continue since they work at an essential business, Fincantieri Marinette Marine.
While some training has gone virtual, other critical training areas require participants to be onsite. Here are a few of the steps NWTC has taken to keep students healthy:
- Installed freestanding hand sanitizers in multiple locations at the facility
- Increased the frequency of cleaning of high-touch areas such as doors, restrooms, tables, chairs and counters
- Prohibited gatherings of more than 10 people, which has led to adding more shifts to ensure compliance
- Required individuals to wear a mask while in the facility
- Implemented facility and equipment disinfection prior to and immediately following training

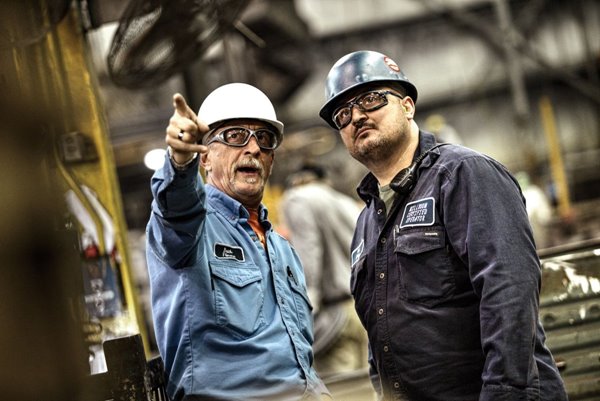