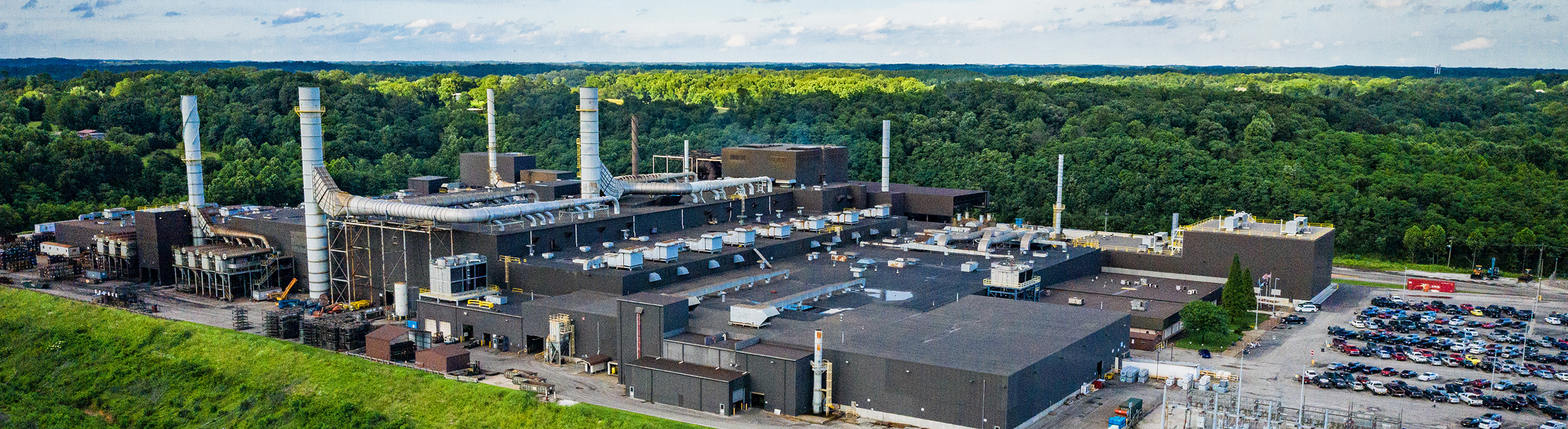
Waupaca Foundry Wins Better Project Award
US Department Of Energy Recognizes Iron Casting Supplier For Energy Innovations
(Waupaca, WI) June 10, 2020—Waupaca Foundry is the recipient of the 2020 Better Project award from the U.S. Department of Energy's Better Plants program for innovations at its Tell City, Indiana plant. The federal program recognizes manufacturers for creating and implementing industrial energy and water efficiency projects, as well as renewable energy and energy resiliency projects.
"Better Plants partners are implementing innovative energy efficiency solutions in the industrial space that are cutting costs and energy use and the Better Practice and Better Project awards honor their leadership," said Valri Lightner, deputy director, advanced manufacturing office, U.S. Department of Energy.
The plant designed and installed a system to remove humidity from the air around the plant's cupola, the furnace used to melt metal. Plant engineers installed a desiccant cupola blast air drying system that removes water vapor from ambient air prior to preheating in the foundry's melt tower. Removing humidity from the air stabilizes operations throughout the year and reduces energy consumption.
"The system passes air through a desiccant air wheel which works like a filter to remove water from the air, increasing the efficiency of the combustion process," said Marco Gonzalez, corporate energy manager for Waupaca Foundry. "It's like if you're trying to light a barbecue during a rainy day, the moisture in the air will consume power from your charcoal and they will take longer to light. By removing the moisture from the air, the fuel can burn more efficiently."
The project reduces foundry coke use, which is the fuel used in the melt furnace, and improves melting efficiency, in turn offsetting rising material costs. Furnaces melt the iron and maintain temperatures ranging from 2,600 to 2,800 degrees Fahrenheit. Computerized systems constantly monitor temperature.
"The system allows us to avoid weather variations in the process of melting iron, especially in our southern locations. Sustained humidity levels at this plant can have monthly averages of 80%, and several days at 100% humidity," Gonzalez said.
According to Waupaca Foundry President, COO and CEO Mike Nikolai, energy conservation is a key strategy. "Our commitment to environmental responsibility moves beyond regulatory compliance to ensure our long-term sustainability. Initiatives like these create value that benefits our customers, shareholders, employees, suppliers and the public," Nikolai said.
The process to melt iron represents 65% of the total plant's energy usage, with coke being the largest energy source. Reducing energy consumption in this process is consistent with Waupaca Foundry's sustainability goals by reducing energy and water consumption, implementing pollution control technologies, and recycling used foundry sand.
The melt process has also realized additional innovation with energy conservation efforts. Excess "waste" heat from the cupola furnace supplies building heat and domestic water heating for Waupaca Foundry facilities during the cold winter seasons. Heat recovery systems used at Waupaca Foundry plants provide 70% of the plants' space heating requirements, and 100% of the plants' hot water needs.
Waupaca Foundry has been recognized by state and federal organizations for implementing sustainability initiatives and providing outstanding leadership in integrating sustainable business practices throughout its manufacturing operations. Those initiatives include:
- Reducing water use and wastewater treatment in key areas of manufacturing production. Plant upgrades substituted single-use water cooling systems with closed loop and air cooled heat exchangers. As a result, demands for water have been cut 66% and non-contact cooling water discharge has been reduced to near zero.
- Waupaca Foundry recycles 450,000 tons of foundry byproducts annually. Sand that can no longer be recycled is used in general construction, road construction, agricultural use, and geotechnical fill.
- Air pollution control uses bag house air filtration and filter leak detection to maintain the highest pollution controls in the foundry industry.
###